Fare di più con meno è il mantra che da sempre caratterizza il comparto birra. Nel rapporto annuale sullo stato e sui progressi del settore in materia ambientale, WRAP traccia le linee guida per il miglioramento della sostenibilità delle birrerie britanniche. Questi suggerimenti devono far riflettere anche i produttori italiani.
Ogni anno, WRAP, l’organizzazione britannica che, analogamente al nostro CONAI, si propone di favorire il riciclo e di creare un mercato per i materiali riciclati, affianca aziende, persone e comunità interessate a ridurre i rifiuti, sviluppare prodotti sostenibili, utilizzare le risorse in modo efficiente. Un altro dei suoi compiti è analizzare i diversi comparti industriali per sottolinearne i progressi ambientali ed evidenziare le aree di miglioramento. Particolare interesse ha riscosso il recente report sul comparto birra che in Gran Bretagna ha una frammentazione simile a quella riscontrabile in Italia, con oltre 700 aziende e una forte preponderanza di microrealtà artigianali. Per i segmenti produttivi più importanti(microbirrerie, birrerie industriali che confezionano bottiglie o lattine ed aziende che si occupano solo di barilotti da 30 litri e oltre), lo studio visualizza graficamente input, processi produttivi e rifiuti/ perdite di risorse.
Le perdite di prodotto
Uno degli sprechi facilmente riducibili è costituito dai 300 mila ettolitri di birra persi ogni anno per inefficienze durante il riempimento di bottiglie e lattine. Le lattine sotto o sovra-riempite non sono recuperabili, perché chiuse prima della verifica del peso e delle stazioni di controllo qualità. Il riempimento non conforme (insufficiente o in eccesso) è in genere riconducibile a scostamenti attribuibili alla riempitrice e più in generale alla linea. Il sistematico controllo del monoblocco, della taratura e della bilancia consentono di lavorare entro le tolleranze stabilite dalla disciplina metrologica e non costringono l’azienda a cautelarsi riempiendo costantemente in eccesso. Le piccole variazioni di volume sono monitorabili e se dovute ad errori umani si può intervenire formando e motivando gli operatori di macchina. Gli scostamenti ripetuti e significativi sono invece attribuibili a problemi tecnici, correggibili con interventi di manutenzione in uno o più punti dell’impianto. Una seconda fonte di spreco di prodotto è la breve shelf life della birra confezionata nei fusti per la spina. La soluzione viene dal fare squadra con i clienti e ipotizzare previsioni di vendita attendibili che non inducano a produrre per il magazzino. I nuovi fusti in plastica che prolungano la shelf life sono ad oggi solo monouso. Il loro mancato riutilizzo, a prima vista, vanifica i benefici derivanti dal minor spreco di prodotto, ma, se adottata in particolari contesti, questa soluzione è comunque ambientalmente vantaggiosa.
Il confezionamento
Per l’alleggerimento delle bottiglie di vetro e delle lattine si può parlare di obiettivo raggiunto. I risultati variano da azienda ad azienda e in alcuni casi la percentuale di riduzione potrebbe salire ancora di qualche punto adottando alcune best practice. Il profilo delle bottiglie impatta sulle perdite di prodotto riconducibili a un riempimento difficoltoso. Il collo lungo e stretto facilita la formazione di schiuma con conseguente uscita della birra, la scelta di bottiglie con una sagoma meno slanciata favorisce lo scorrimento lungo le linee e consente un riempimento più pulito. I grandi fusti di plastica (HDPE e PET) sono una delle principali innovazioni nel packaging birrario: a vuoto pesano meno della metà dei loro corrispondenti in acciaio; sono monouso, ma in alcune circostanze hanno dei benefici ambientali tali da renderli competitivi con i fusti ri-riempibili, per esempio quando i tragitti sono lunghi, quando sono utilizzati per eventi e soprattutto quando il cliente è impossibilitato a restituire i vuoti (situazione riscontrabile nell’export). Il loro garantire un prolungamento della shelf life apre agli imbottigliatori nuove opportunità di mercato soprattutto all’estero. Ad oggi, non esistono approfondite comparazioni sulle reali emissioni di C02 attribuibili a queste due alternative, manca in particolare un’analisi del ciclo di vita che includa anche il lavaggio resi. Si è ipotizzato che la produzione di un fusto monouso da 30 litri in PET comporti emissioni pari a 1,7 kg di C02 per hl, contro 1,4 kg C02 per hl emessi per la pulizia di un fusto acciaio di pari dimensioni; non è invece noto il risparmio di carburante sui lunghi percorsi, valutato in funzione del minor peso dei fusti di plastica ed in considerazione dell’assunto che non sempre il mezzo di trasporto rientri vuoto. Per le birre in lattina o in bottiglia un’ulteriore possibilità di risparmio di risorse può venire da una maggiore attenzione all’estensibile impiegato per stabilizzare i bancali. Secondo WRAP si potrebbero risparmiare fino a 1,45 milioni di sterline.
L’acqua
L’efficienza dello sfruttamento dell’acqua è notevolmente aumentata, anche se non tutte le aziende operano secondo le best practice. Per produrre mezzo litro di birra si utilizzano in media 2,5 litri di acqua (1,7 per le aziende che operano secondo le buone pratiche di settore), nel 1990 l’utilizzo superava i 3,8 litri. Se l’intero settore riuscisse a ridurre i consumi del 10%, risparmierebbe 660 milioni di litri, di acqua, pari a 2 milioni di sterline/ anno. Una ricerca del BBPA (British Beer and Pub Association) mostra che molte birrerie hanno già raggiunto il picco dell’efficienza nello sfruttamento dell’acqua, ulteriori miglioramenti potranno venire solo da una reale innovazione. Una potenziale area di miglioramento deriva da un più puntuale monitoraggio. Oggi si controllano solo la quantità immessa in produzione e la quantità smaltita a fine processo, pochi si premurano di sapere quali fasi determinano i maggiori utilizzi o sprechi e di impostare un piano di miglioramento.
Una piccola perdita da una valvola di una torre di raffreddamento costa all’azienda fino a 3,5 sterline /ora. In mancanza di un controllo può durare a lungo e costare più di 2.500 sterline/ mese. Una buona gestione dell’acqua consente saving anche in aree ad essa correlate, soprattutto se le perdite riguardano le fasi finali del processo. Si riducono l’energia per pompaggio, riscaldamento e raffreddamento, eliminazione dei reflui, trattamenti chimici e fisici dell’acqua in sé e delle acque di scarico. Il processo a maggior incidenza è la pulizia, soprattutto di serbatoi, botti e imballaggi primari a rendere.
I consumi variano da azienda ad azienda; con impianti poco automatizzati si consumano fino a 45 litri di acqua per ogni litro di birra confezionata; negli impianti automatici l’impiego di detergenti e di cicli chiusi consente un notevole risparmio. Con gli imballaggi monouso i consumi si riducono, ma l’impatto ambientale può ripercuotersi su altre voci. Prima di decidere è necessario valutare l’intero ciclo di vita del prodotto.
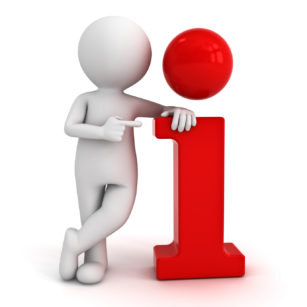
- migliorare il monitoraggio dei consumi di acqua in generale e nei sistemi CIP in particolare;
- migliorare i sistemi CIP adeguandoli all’innovazione tecnologica;
- formare il personale perché li utilizzi con la massima efficacia ed efficienza;
- monitorare monoblocchi e linee di confezionamento per prevenire le perdite di prodotto;
- manutentare le attrezzature;
- applicare una corretta movimentazione dei contenitori vuoti e pieni;
- evitare di far rientrare le acque reflue nei parametri accettabili di COD e pH limitandosi a diluirli con acqua potabile;
- smaltire i residui solidi destinandoli alla mangimisitica e per i residui organici che restano nelle acque ricorrendo alla digestione anaerobia;
- prestare attenzione all’uso e alle prestazioni dei film estensibili che stabilizzano i bancali;
- tenere alta l’attenzione sul riciclo e sulla sostenibilità.
I sistemi CIP
I sistemi di lavaggio in CIP sono un’altra voce che incide sul consumo di acqua. Secondo la Carbon Trust’s guide, verificando i reali tempi di lavaggio, le birrerie britanniche potrebbero risparmiare l’1% delle annuali emissioni di C02 (4.600 t). È inoltre possibile migliorare l’efficienza dei sistemi CIP ottimizzandone progettazione e layout; dotandoli di ricicli interni di acqua e detergenti per minimizzare i reflui; rimuovendo i residui di birra e di contaminanti solidi prima di avviare il lavaggio automatico; assicurando che il serbatoio che contiene la soda sia dimensionato in modo da non prevedere rabbocchi e conseguenti perdite mentre il sistema è in funzione; impostando programmi operativi corrispondenti alle reali esigenze di sanificazione degli impianti; formando adeguatamente il personale. Alcuni sistemi CIP multielementi raggiungono una considerevole complessità; se installati da tempo layout ed efficienza dovrebbero essere riconsiderate per capire se ci siano margini di miglioramento e se sia necessario rafforzarli o sostituirli.
Le acque di scarico
Le acque in uscita delle birrerie hanno un elevato COD (2000 – 6000 mg/l ed oltre), nonché un rapporto BOD/COD compreso tra 0,5 – 0,74. Contengono infatti composti organici (zuccheri, alcol etilico, amidi) biodegradabili con tecniche aerobie o anaerobie. Ciò nonostante molte birrerie britanniche scaricano tuttora nelle fognature acque non trattate. L’impatto ambientale di questa pratica è difficilmente calcolabile a causa delle diverse dimensioni ed abitudini aziendali; fra queste la pratica di diluire gli scarti con acqua potabile prima della loro eliminazione.
Residui solidi organici
Ciò che resta del malto è da sempre destinato alla mangimistica, anche se negli ultimi anni si è provato a percorrere strade diverse. Gli altri due residui solidi organici sono lievito e luppolo. I lieviti non possono essere utilizzati come ingredienti dei mangimi per ruminanti, ma hanno un elevato valore nutrizionale ed economico nella mangimistica degli animali monogastrici (soprattutto suini) e nell’alimentazione umana. I residui di lievito si deteriorano in breve tempo e sono pertanto denaturati prima del reimpiego come materie prime secondarie. La produzione è su vasta scala e l’essiccamento di malto e lievito prima del trasporto riduce i volumi movimentati e ne allunga la shelf- life. Il luppolo è amaro, gli animali non lo gradiscono e ha pertanto poco valore per gli agricoltori. In UK, la quantità residua dopo la lavorazione della birra supera le 10 mila tonnellate all’anno. Le microbirrerie usano il luppolo tal quale, difficile da recuperare; le birrerie industriali usano i pellets recuperabili insieme al malto. Il luppolo usato al naturale rispecchia a pieno la tradizione birraria, ma la sua resa ambientale è scarsa. Una delle grandi sfide è trovare un modo efficace ed efficiente per riutilizzarlo, se non altro come compost o fertilizzante.
Lo sfruttamento come biomasse
I residui solidi organici sono fonti di energie rinnovabili. Il malto ha un alto potere calorifico (20.7-21.9 MJ/kg), ma questo impiego lo distoglie dalla mangimistica; le acque di scarico sono una fonte meno efficiente e meno pregiata di bioenergia, per alimentare gli impianti devono infatti essere rafforzate con residui solidi. La digestione anaerobica, oggi poco diffusa, è una valida alternativa alla mangimistica. Le barriere all’ingresso sono alte; il grande ostacolo, tale da vanificare i benefici ambientali, è il conferimento del materiale ai pochi impianti esistenti. Alcune grandi birrerie hanno peraltro deciso di costruire propri digestori nei pressi degli stabilimenti.