Rappresenta una delle più antiche distillerie artigianali e fabbriche di liquori italiane, la Casoni Fabbricazione Liquori S.p.A. di Finale Emilia, nel Modenese, fondata oltre duecento anni fa come piccolo opificio familiare, nel lontano 1814.
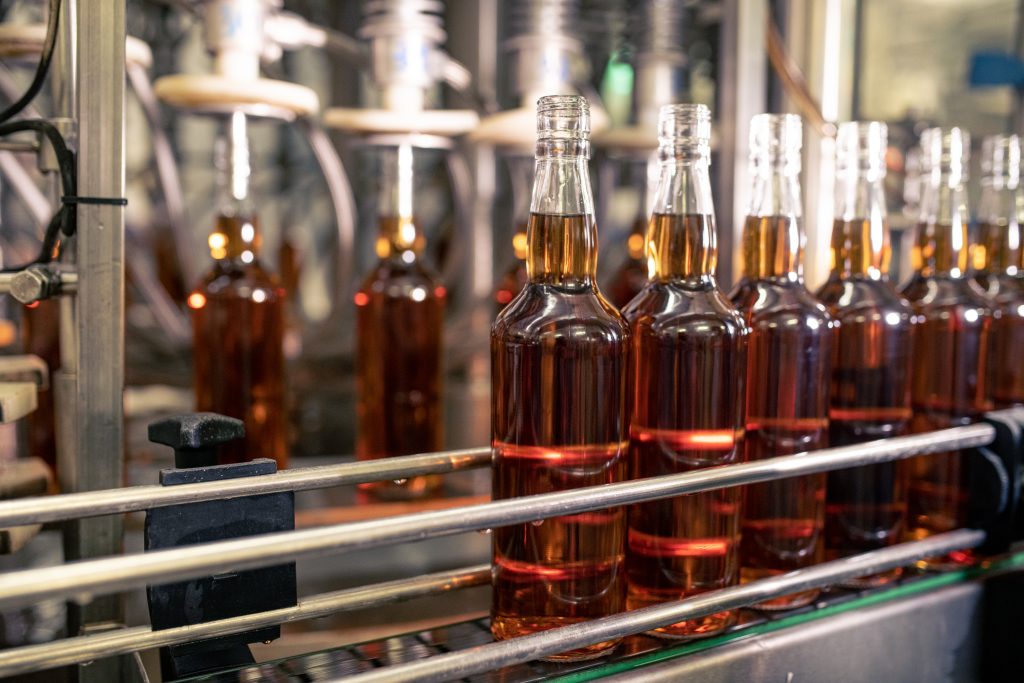
La qualità dei liquori e distillati tipici del territorio – tra cui Anicetta, Anicione, Rosolio e Acquavite d’Anice –, unita allo spirito d’iniziativa del fondatore Giuseppe Casoni, hanno condotto l’azienda sulla strada del successo attraverso i decenni e le generazioni, passando per le due guerre mondiali e le varie passioni dei titolari. Tra le più importanti, è nota la carriera automobilistica di Mario Casoni, pilota capace di segnare cinquant’anni di storia dell’automobilismo italiano e, contemporaneamente, imprenditore illuminato, che ha saputo portare la fabbrica familiare al successo internazionale. Tradizione e know-how sono i valori cardine della Casoni, che ha sempre scelto di impiegare materie prime ottimali, ricercando senza sosta nuove combinazioni e – priorità assoluta – portando avanti una produzione completamente naturale tramite infusioni e distillazioni di erbe, bacche e frutti, il che ha contribuito a dar vita a referenze “buone e genuine”, uniche e caratteristiche, veri e propri valori aggiunti per il cliente finale. Dopo l’alternarsi di diverse proprietà, l’azienda è tornata nelle mani della famiglia: Paolo Molinari, nipote di Mario, insieme a una cordata di imprenditori nel 2016 ha riacquisito la storica distilleria di famiglia.
«Il nostro punto di forza è quello di essere riusciti a rimanere flessibili e reattivi – spiega Molinari, Amministratore di Casoni Fabbricazione Liquori S.p.A. – per andare incontro alle sempre mutevoli richieste di mercato. Oggi Casoni si propone sulla piazza nazionale e internazionale dei liquori con una rinnovata brand identity, che rispecchia l’essenza di un’azienda storica e legata al territorio, ma animata da un continuo fermento. Ne sono testimonianza le tante novità di prodotto nate per rispondere alle tendenze di un settore sempre più creativo e innovativo e per far progredire il mondo del bartending italiano».
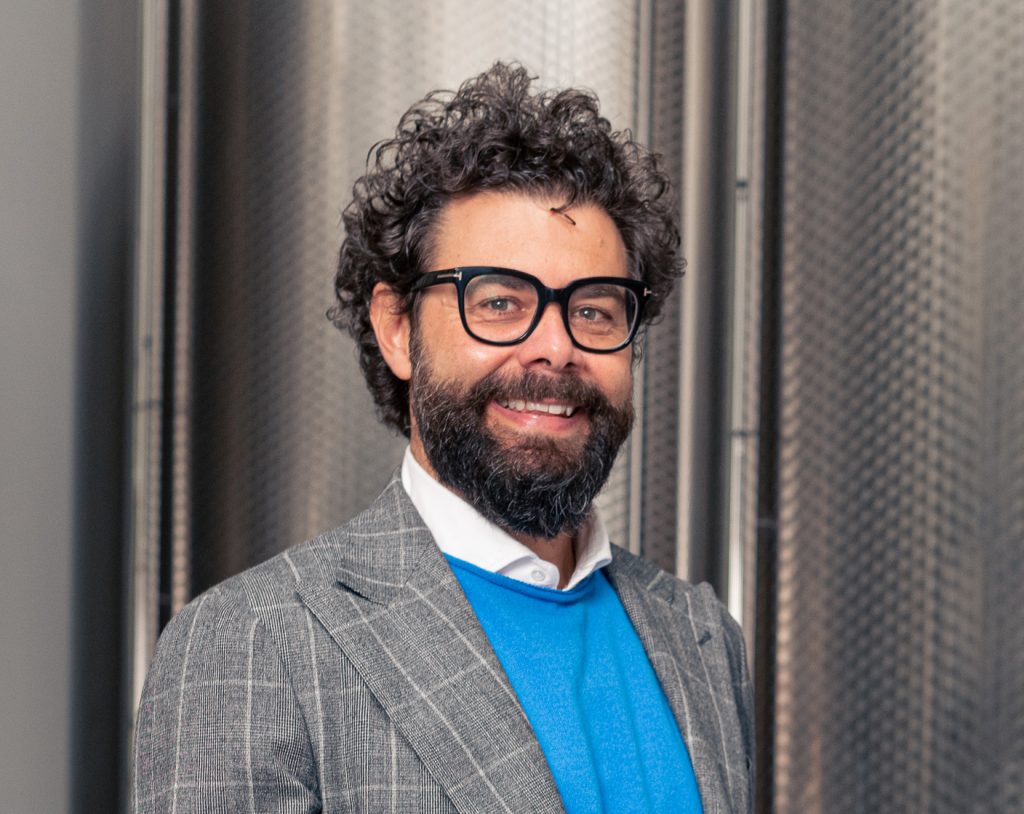
Oltre cinque milioni di investimenti
La distilleria, che da qualche anno ha anche una partecipazione di maggioranza in uno stabilimento di produzione in Slovacchia e una società di distribuzione nel Regno Unito, nella sua fabbrica finalese può contare su circa 70 dipendenti. Nell’ultimo triennio sono stati investiti oltre cinque milioni di euro per ammodernare il parco macchine – principalmente quelle destinate all’imbottigliamento e al confezionamento –, per realizzare una nuova sala di produzione completamente automatizzata e per l’acquisto di un nuovo magazzino a uso logistico. Due, attualmente, sono le sale di produzione, oltre a una sala di infusione e distillazione dove, partendo direttamente dalle erbe, vengono realizzate le basi aromatiche utilizzate per i diversi prodotti; l’impresa comprende poi svariati magazzini e depositi e una sala di imbottigliamento e confezionamento. In quest’ultimo comparto sono presenti tre linee completamente automatizzate, oltre a una linea per prodotti ready to drink, una linea per la produzione e il confezionamento di mignon e una linea semiautomatica “estremante versatile”, che consente, senza la necessità di costosi attrezzaggi, di ultimare contenitori delle più svariate forme e capacità.
«La tecnologia applicata all’imbottigliamento e al confezionamento è una componente di fondamentale importanza nel nostro settore per poter garantire standard di qualità e sicurezza sempre più alti»
«La tecnologia applicata all’imbottigliamento e al confezionamento è una componente di fondamentale importanza nel nostro settore per poter garantire standard di qualità e sicurezza sempre più alti»
«Se ci focalizziamo sulle tre linee automatiche principali, quelle che hanno prodotto la maggioranza dei 30 milioni di bottiglie realizzate e vendute nel corso del 2023, sono state ammodernate nel corso dell’ultimo triennio – chiarisce Molinari –: abbiamo inserito due etichettatrici PE, due incartonatrici Wrap around Baumer, due piani di accumulo motorizzato Europool, un depallettizzatore FMT – oltre a uno OMA, che si aggiungerà a breve –, due ispezionatori ottici per il controllo delle bottiglie vuote Heuft, due sistemi di controllo livello e corretto posizionamento del tappo Heuft, un fasciatore per pallet Robopac, un pastorizzatore flash di Sordi e un impianto di dosaggio Velcorin di Lanxess».
Ispezione, sciacquatura, riempimento
Il viaggio dei nuovi contenitori in vetro sulle linee di imbottigliamento ha inizio dal depallettizzatore automatico, che fa in modo che le bottiglie vengano organizzate in un’unica fila passando attraverso una serie di nastri trasportatori a velocità variabile; tutti i nastri trasportatori sono gestiti da inverter, così che, per ogni formato bottiglia, venga memorizzata la velocità dei nastri sul PLC di un apposito quadro di gestione. Questo consente di ridurre i tempi normalmente necessari alla messa a punto della linea in seguito a ogni cambio formato, considerando che in azienda vengono lavorati oltre 70 formati bottiglia differenti per forma, capacità e imboccatura e che, quotidianamente, è necessario effettuare uno o due cambi attrezzature. Una volta che le bottiglie transitano sul nastro trasportatore monofilare, esse proseguono all’interno di un’ispezionatrice ottica Heuft per verificare, con diverse telecamere, che abbiano le giuste dimensioni, un’ideale imboccatura e che non presentino difetti estetici o funzionali, oltre a non essere contaminate dalla presenza di corpi estranei o residui liquidi. Dopo aver superato i molteplici controlli a telecamera, se la bottiglia non viene scartata si presenta all’ingresso di un monoblocco Enoberg che, dopo averla capovolta, la risciacqua con acqua demineralizzata, la soffia con aria microfiltrata – entrambi i trattamenti vengono effettuati a pressioni e micrometrie definite e controllate – e, dopo averla nuovamente raddrizzata, provvede a riempirla con un sistema in leggera sovrappressione, gestito da un trasduttore e personalizzato in base a ogni tipologia di bottiglia o prodotto che verrà confezionato. In uscita dal monoblocco di sciacquatura, soffiatura e riempimento, la bottiglia è quindi sigillata con tappatori Kompass, macchine in grado di eseguire quest’operazione impiegando molteplici chiusure differenti.
Dalla tappatura all’incartonamento
In uscita da ogni tappatore, un sensore controlla la presenza del tappo sul vetro, mentre un ulteriore sistema di controllo Heuft monitora il corretto livello di riempimento e il giusto posizionamento della capsula applicata, per verificare che la personalizzazione sia quella ottimale per il prodotto in lavorazione e che, banalmente, il pantone della capsula sia idoneo nel caso in cui la stessa non sia customizzata. Quando risulta non necessario applicare una capsula PVC termoretraibile, la macchina Nortan dedicata a quest’operazione viene bypassata e si arriva direttamente alla fase di etichettatura.
«Le etichettatrici PE acquistate – afferma Molinari – sono in grado di applicare sia le etichette autoadesive che le etichette colla a freddo, oltre, naturalmente, ai molti contrassegni di Stato dei diversi Paesi per i quali produciamo. Un sistema ottico di controllo all’ingresso della macchina assicura il giusto orientamento delle bottiglie, affinché le stesse si presentino correttamente davanti a ogni stazione di etichettatura e stiratura». Sempre all’interno della macchina, un marcatore Nimax permette l’applicazione del lotto di produzione in posizioni che variano in funzione della grafica e del layout dell’etichetta, mentre un ulteriore sistema a telecamera, posto all’uscita dell’etichettatrice, verifica il posizionamento dell’etichetta del prodotto in lavorazione e la presenza, o meno, dell’eventuale contrassegno di Stato. Qualora il sistema ottico di controllo dell’etichettatrice verifichi un difetto, si provvede a scartare la bottiglia su un piano motorizzato posto dopo l’etichettatrice; se il processo procede senza inghippi, invece, le bottiglie proseguono il confezionamento verso i wrap around Baumer, che in scatole da 6 o 12, con o senza l’applicazione automatica di alveari, terminano il confezionamento dei cartoni, incollati intorno al pacco bottiglie precedentemente formato in macchina.
La tecnologia? Di fondamentale importanza
Ogni cartone uscente dai wrap passa sopra a una bilancia, che verifica il peso della scatola; tramite nastri di trasporto che salgono e scendono, i cartoni vengono marcati con le indicazioni richieste da clienti e normativa, tramite resina fusa – con applicatori Markem – o etichette applicate in modo automatico grazie ai sistemi di stampa e applicazione Nimax. Proseguendo la corsa su molteplici nastri di trasporto, i vari cartoni passano alla fase di pallettizzazione tramite tre differenti pallettizzatori – uno per ciascuna linea automatica di produzione –, che provvedono a orientare correttamente le scatole affinché la disposizione prevista dallo schema di pallettizzazione sia quello desiderato per il dato formato, creando il pallet come richiesto dalle specifiche di lavoro. I pallet, una volta terminati, attraverso rulliere e ralle motorizzate di transito giungono alla stazione di fasciatura, dove un braccio motorizzato assicura che vengano avvolti da film estensibile e sigillati tramite un top di materiale plastico. Ultimo step che interessa i pallet prima di giungere a magazzino è la stazione di stampa e applicazione delle due etichette logistiche, le quali, poste su due lati adiacenti, permettono di ottenere tutte le informazioni in chiaro e in EAN code per la corretta gestione FIFO (first-in, first-out) del magazzino e dei prodotti confezionati.
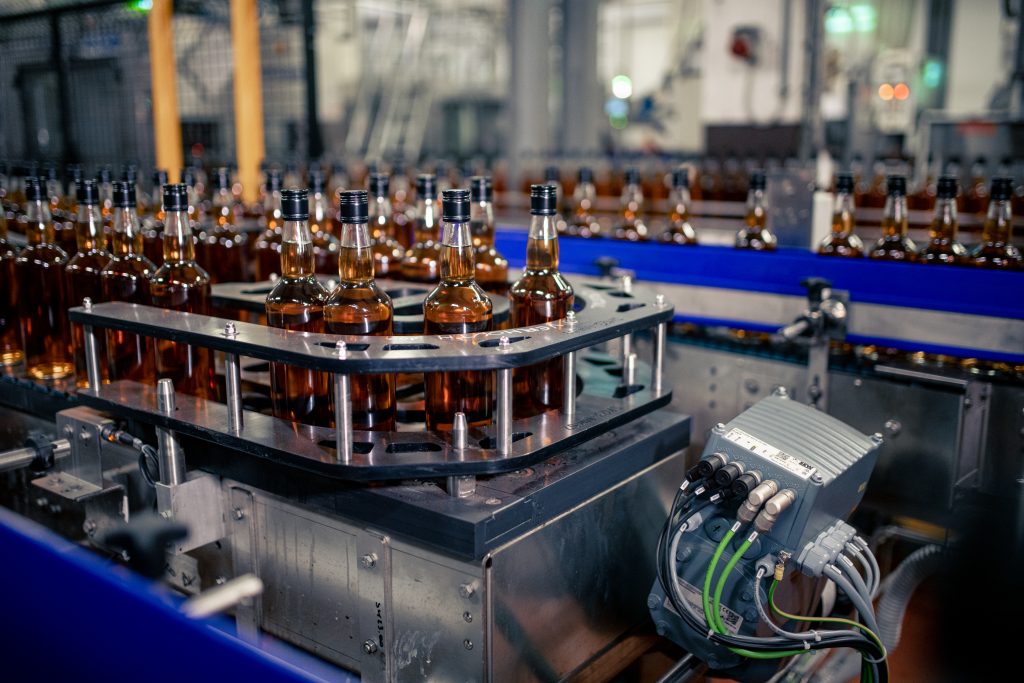
«Una delle tecnologie più avanzate che abbiamo recentemente acquistato è il sistema di controllo delle bottiglie vuote, il quale, tramite ben dieci telecamere ad alta definizione e un apposito software di gestione, è in grado di rilevare il più piccolo difetto e/o corpo estraneo eventualmente presente nella bottiglia, scartandola con un’ottima riproducibilità e un minimo “falso scarto” – assicura l’AD di Casoni Fabbricazione Liquori S.p.A. –. La tecnologia applicata all’imbottigliamento e al confezionamento è una componente di fondamentale importanza nel nostro settore, per poter garantire ai consumatori standard di qualità e sicurezza sempre più alti, soprattutto nell’industria alimentare. I controlli statistici di processo che gli addetti alle linee di produzione effettuano durante l’intero ciclo produttivo si devono aggiungere ai controlli che i sistemi automatici eseguono in maniera costante».